Caterpillar Gives Miners an Inside Look at Technology
June 22, 2017 - Nearly 75 miners representing almost 25 global companies were recently given an inside look at Cat® technologies for mining during a two-day Mining Technology Demonstration & Program at the manufacturer’s Tinaja Hills Demonstration & Learning Center near Tucson, Arizona.
Hosted by their Cat dealers, attendees saw a customized technology demonstration that featured Cat autonomous trucks and dozers working alongside manned vehicles. The program also included in-the-iron time as well as presentations on Cat MineStar™ delivered by technology leaders and subject matter experts. MineStar is a suite of offerings for the mining industry that are part of the company’s Cat Connect family of technologies and services.
Autonomous Loading and Hauling
The autonomous loading and hauling portion of the demonstration featured three Cat trucks — two manned and one autonomous — being loaded by a Cat 6060 Hydraulic Shovel. The autonomous 793F, equipped with Cat Command for hauling, was being controlled from the new MineStar Command Center located on the demonstration site.
The shovel operator was using Cat Terrain for loading, a machine guidance system, to set the spot point for the autonomous truck and tell the truck when to leave. The in-cab Terrain screen lets the loader operator “see” the truck — where it’s currently located, where it will be traveling next, the payload it’s carrying and even the grade of ore in the bed.
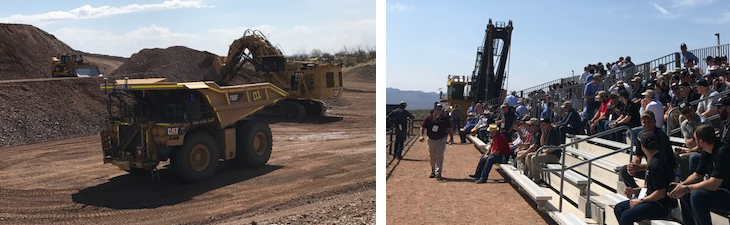
After being loaded, the autonomous truck headed to the dump site, where a pre-programmed script directed the truck to slow as it neared the ledge, stop when it reached the berm, raise the bed, wait a predetermined time to allow the material to sheet, and then drive away while lowering the bed. Attendees learned that the timing of this sequence can be adjusted for different conditions. For example, if conditions were wet and the material was sticky, the script could be written to allow more time for the load to dump from the truck.
The autonomous truck also encountered several hazards on the roadway to showcase some of Command’s safety features, such as the Lidar system located on the front of the truck. This system contains 64 lasers that gather millions of data points every second, giving the truck a rich view of its environment. During the demonstration, the truck came to a complete stop when it identified a light vehicle and a mannequin that were placed in its path on the haul road.
The program also demonstrated an “A-stop” or “all-stop” — a device carried by personnel on site that will stop all trucks within 300 meters (984 feet). One audience member had the opportunity to demonstrate the A-stop controller, stopping the autonomous truck at the push of a single button.
During the demonstration, attendees also heard about expansion plans for the Command for hauling product. While the 793F is the flagship autonomous truck, with more than 60 in operation around the world, Caterpillar is expanding Command to work on Cat 789D and 797F trucks as well as machines from other manufacturers, such as the Komatsu 930E-4SE.
Autonomous Dozing
While manned and autonomous trucks traveled the haul road from the shovel to the dump site and back again, an autonomous Cat D11T Dozer equipped with Command for dozing worked alongside them during the demonstration, pushing dirt for the shovel to dig and load.
The demonstration included two types of automated dozing — line-of-sight remote control and non-line-of-sight operation from the Command Center.
The line-of-sight control is delivered by an over-the-shoulder console designed for short-duration activities like cleaning up under highwalls or stabilizing slides. During the demonstration, the operator stood near the top of the grandstand where attendees were seated, operating the machine using controls that are identical to what he would be using in the cab.
The remote operator station enables the operator to work from a comfortable, seated position — also with familiar dozer controls — and is ideal for full-shift operations. A live feed to the grandstand allowed attendees to see the dozer in action while also watching the operator in the control center, where he had access to a complete picture of the machine’s working environment delivered by high-definition cameras and a microphone mounted on the machine.
While not shown during the demonstration, the presentation included information on semi-autonomous dozing, which uses the remote operator station to allow a single operator to take command of multiple dozers while located across the mine site, or even across the world.
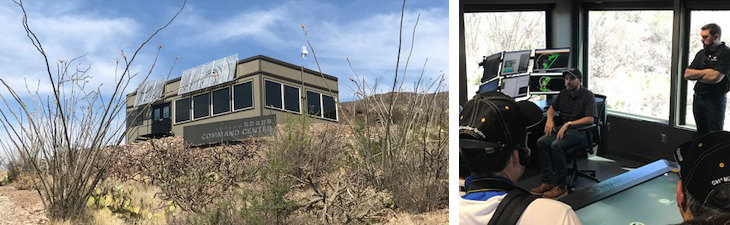
Products and Services
In addition to the demonstration, program participants also heard updates on Cat technology products and services for mining.
The opening session included a presentation called “What Do Miners Care About,” during which two Caterpillar mining technology leaders discussed some of the biggest challenges in the industry and the technologies that can help address them.
“We understand that our customers are looking for consistency across their operations, reductions in cost, getting the maximum output from all of their assets,” said Craig Watkins, a Caterpillar mining technology manager. “We’re committed to helping them use Cat technologies to achieve those goals. And we’re also bringing in the right technology partners to ensure we can do that across the mine site, and across the mining enterprise.”
For example, Caterpillar has partnered with Trimble to help mines better manage their overall businesses. This collaboration leverages Caterpillar industry expertise and its MineStar suite of technology products along with Trimble’s Connected Mine™ platform. This platform integrates data from the mining enterprise and feeds it to the mine’s ERP system, providing one single data source for multiple sites. It also stores historical data to allow seamless technology transitions.
“Basically, this partnership allows miners to have the information they need to make better-informed business decisions,” said Watkins.
Additional partnerships include Maptek, a mine planning system that requires less human interaction and reduces human error, and FTP Solutions, which provides end-to-end network and infrastructure monitoring for Cat technology applications like office, servers, switches and onboard components.
Caterpillar also has working relationships with what it calls integration partners. “These relationships allow us to enhance our offerings across the value chain and ensure interoperability across multiple platforms and mixed-fleet environments,” explained Bill Dears, a Caterpillar commercial mining manager.
These partners include providers of Enterprise Resource Planning (ERP) data management and reporting tools, such as JD Edwards and SAP, as well as site network communication providers like CISCO, Siemens and Extreme Networks.
The presenters also discussed the return miners can expect from their investment in Cat technologies.
“This is the exciting part,” said Watkins. “We have countless examples from our customers on how quickly they are achieving a Return on Investment (ROI) from their Cat technologies, and four months seems to be a magic number. We aren’t promising that, of course, but it does seem to be a sweet spot. Once you’ve gotten your ROI, it’s all upside from there. And when we bring in consulting services, we can help customers get even more value.”
Dears explained the impact these technologies can have on the overall mining business. “Our entire suite helps you manage your costs,” he said. “And when you better manage costs, you’re going to be more profitable.”
Additional presentations covered specific Cat technology products and services for mining, including:
- Fleet, an integrated fleet monitoring and management system that works with all types of assets and equipment and shares data with other Cat technologies.
- Terrain, a machine guidance technology with offerings for grading, drilling and loading.
- Detect, which incorporates a number of products to enhance safety, including Vision, Object Detection, Personnel for Longwall, Proximity Awareness and Fatigue Risk Management Solutions.
- Health, which includes the onboard hardware used to extract machine data from Cat and non Cat equipment; an office application that monitors alarms, events and productivity; and a laptop software that can be used to view and manage data.
- Cat Equipment Care Advisor, an application that automates the use of analytics and combines it with expert equipment knowledge to enable Cat dealer Condition Monitoring services.
- Command, which in addition to the hauling and dozing applications shown during the demonstration, also includes automation products for drilling and underground load-haul-dump applications.
- Mining Professional Services, which provides consulting services that focus on the mining business beyond machines. Caterpillar experts helps miners apply technologies and data analysis to capture the maximum value from their operations.