Cat® Autonomous Haulage System Users Report Productivity & Safety Gains
January 16, 2018 - The autonomous haulage system that Caterpillar developed in partnership with several of its largest mining customers in the last decade has been successfully deployed for over five years, and in that time has safely moved more than 600 million tonnes (661 tons) of ore. While the team at Caterpillar has been quick to point out the benefits of the system, its customers are now beginning to publicly share the scale of what autonomy is making possible in their operations.
“They’re sharing it by reporting actual results — like a 20 percent increase in overall productivity,” says John Deselem, Caterpillar technology manager responsible for the company’s autonomous haulage product. “They’re also sharing it through expansions — adding more autonomous trucks to current operations and introducing autonomy on additional mine sites. This system is having a significant impact on these mining operations — so much so that they want to replicate it elsewhere.”
Caterpillar’s flagship autonomous operation, the Fortescue Metals Group (FMG) Solomon iron ore mine in the Pilbara region of Western Australia, recently announced that it will expand on the nearly 60 autonomous trucks operating at Solomon. At its Chichester Hub, FMG will retrofit the system on approximately 100 Cat trucks and — in order to meet the company’s business needs — Komatsu truck models, as well.
Elsewhere in the Pilbara, BHP Billiton recently announced that its Jimblebar operations will become its first operation to move completely to driverless trucks, expanding its current fleet of 25 Cat 793F autonomous trucks to 50 by the end of 2017. The company has reported that the move to automation is part of its strategy to improve safety, build capacity and remain globally competitive.
Changing How Material is Moved
The Cat autonomous haulage system, Command for hauling, is part of the company’s Cat MineStar™ suite of technology products for the mining industry. Caterpillar has Command offerings for drilling, dozing and underground mining, as well.
Trucks equipped with Command respond to calls to the shovel, move into position, haul to dump points and even report for maintenance — all without an operator on board.
“Just a few short years ago, we had a handful of trucks at a customer site, and today we have the single largest autonomous truck fleet in the world,” says Deselem. “We’re changing how mining companies move material. They’re experiencing the consistency that comes from near-continuous operation and the elimination of human error. They’re able to operate with fewer people in potentially hazardous areas. And they’re experiencing unheard-of productivity gains.”
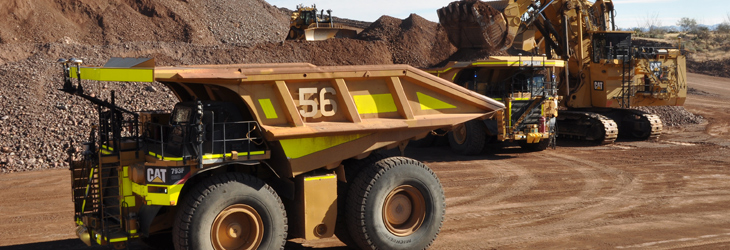
Boosting Safety
Autonomous trucks are able to interact safely with other manned and light vehicles thanks to Command’s multiple, redundant sensing systems. They also maintain optimal operating speeds and safe following distances at all times.
“Of course, the biggest safety benefit is the fact that there are fewer people being exposed to on-site hazards,” says Deselem. “But autonomous trucks are also safer in how they operate. Cat autonomous trucks have moved millions of tons of ore to-date, and that’s all without a single lost-time injury.”
One Caterpillar mining customer recently reported that they’ve experienced a reduction in the frequency of safety incidents by 50 percent. “On top of that, they’re finding that the severity of the few incidents they do have is reduced even more than,” explains Deselem. “The safety benefits of autonomous haulage are just outstanding.”
Increasing Productivity and Lowering Costs
Deselem says there are many contributors to the efficiency and productivity gains realized through autonomous haulage. Mines are able to optimize production, with tight truck exchanges and no need for shift changes. There’s also less damage to machines and downtime due to misuse and overloading.
“The consistency of operations is a huge benefit,” says Deselem. “When we’re more consistent, we’re more efficient. And when we’re more efficient we reduce costs.”
These savings are a big win for mining customers who have had a laser focus on reducing costs in the last five years. “Most of our customers have implemented a variety of technologies to help them cut costs,” says Deselem. “While autonomous haulage is not solely responsible for those reductions, it’s having a significant impact.”
The benefits at Solomon are proven and growing, he says, with FMG reporting a 20 percent productivity boost since the implementation of autonomous haulage just a few short years ago.
“Fortescue values the strategic relationship developed with Cat since 2012, as autonomous haulage technology has been implemented at our Solomon Hub,” said Fortescue Chief Executive Officer Nev Power. “We will continue to work together to ensure the next stage successfully builds on the safety, productivity and efficiency gains we have achieved so far.”
Likewise, BHP’s Jimblebar mine publicly stated the positive impact of the system when announcing the company’s intent to make every haul truck on the site autonomous. “The productivity benefits of the autonomous haulage fleet at Jimblebar have already been demonstrated and help us reduce costs by 20 percent,” said Chief Technology Officer Diane Juergens.
.png)
Working Hand in Hand
While the safety, productivity and cost benefits of autonomous haulage are easy to see, Deselem points out an additional benefit that’s difficult to measure but that Caterpillar believes is essential to the success its customers are having with Command for hauling: the expertise that goes along with the system.
“A lot of these successes are achieved through collaboration — and not just when it comes to the technology itself,” he says. “People and processes must be optimized for and with the use of technology. It takes skilled people to ensure that optimization happens so we can really achieve the full value of the system.”
Deselem says Caterpillar has developed a top-notch team to go along with the Intellectual Property it provides. “We’re on site to implement the system, along with the Cat dealer, and we work hand in hand to fill whatever role they need us to.”
Caterpillar currently has more than 25 personnel at customer sites, fulfilling roles such as site manager, application specialist, builder, controller and site engineer. “Today’s Run Teams have 150 years of combined experience running the autonomous haulage system on mine sites,” says Deselem. “In addition, we have a strong pipeline for these key job roles with 30 people being actively mentored and prepared to take on future site-based roles for our customers.”
With every new Command for hauling implementation, Caterpillar sends its dedicated Deployment Team to supplement the Run Team and help Cat dealers and mine personnel during the startup phase. This additional expertise ensures the most efficient launch of the autonomous system.
In addition to providing on-site personnel, Caterpillar also provides training for dealer and mine site teams. “We have 12 globally based training instructors available to assist in preparing personnel to be effective and safe as they operate the autonomous system,” says Deselem.
While the site-based Run Teams provide direct collaboration and support for the mine site, Caterpillar has more than 40 experts on a broad technology support team who address issues every day. “These people are based in various areas around the world to provide a ‘follow the sun’ approach to support 24/7, so that additional specialized help is only a phone call away,” says Deselem.
Beyond the implementation and support teams, the company also has more than 60 engineers fully dedicated to research, development and validation of the system. In addition, hundreds of engineers support the program ad hoc as needed from their areas of specialty.
“We never stop trying to improve Command for hauling, or any of our other MineStar offerings,” says Deselem. “Our customers expect Cat mining technologies to be world-class and cutting-edge. So we keep looking for the next big thing, that game-changer that our customers need to remain competitive and profitable.”
Technology solutions like Command for hauling are growing at an exponential rate, says Deselem, and the speed at which they are being implemented is growing, as well.
“Our first implementation of autonomous haulage took years — developing the technology in collaboration with our customers, and also working alongside them as we discovered together how best to implement it and manage the on-site changes required to adjust to the new processes,” Deselem recalls. “Our most recent implementation took 10 months. We have a proven technology and proven processes and we’re able to quickly get the system up and running so our customers can begin reaping the benefits.”
Mining companies like Fortescue are prepared to use every technology tool to their advantage. “By harnessing leading-edge technology, supporting the skills development of our workforce and collaborating with our suppliers, we will continue to deliver ongoing cost reductions, ensuring we remain at the lowest end of the global cost curve,” Power said.